2021.02.15
A study of thermal performance change of cryogenic heat pipes by difference of wick structures with wide range of working fluid filling ratio
SOKENDAI Student Dispatch Program program year: 2019
Accelerator science WANISON Ramnarong
加速器科学
A study of thermal performance change of cryogenic heat pipes by wick structures for wide range of working fluid filling ratio
journal: IOP Conference Series: Materials Science and Engineering
DOI: 10.1088/1757-899X/755/1/012109
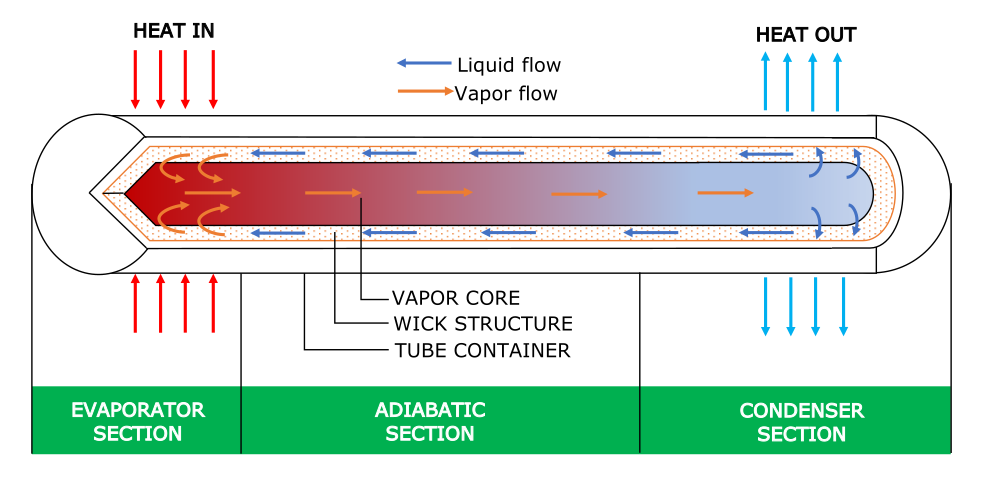
A heat pipe is a tube device whose inner surface is lined with a porous capillary wick that can transfer heat rapidly away from the source. The wick is saturated by the liquid phase of a working fluid and the remaining volume of the tube is occupied by vapor phase. Heat applied externally to the evaporator section is conducted through the pipe wall and the wick structure, where it vaporizes the working fluid in that section. The resulting difference in pressure drives vapor from the evaporator section to the condenser section where it condenses and releasing the latent heat of vaporization to a heat sink in that section of heat pipe. The capillary pressure is developed where depletion of liquid by evaporation causes the liquid-vapor interface in the evaporator to enter into the wick surface. This capillary pressure pumps the condensed fluid back to the evaporator for re-evaporation.
For the practical application such as transmission of electric power and superconducting magnets operating above 20 K, development of the high-temperature superconducting technology is being promoted in many countries. Superconducting technology requires efficient cooling. Among various cooling method, cryogenic heat pipes have attracted considerable attention in the area of spacecraft cooling and superconducting magnets cooling due to its high reliability, small size, low weight, no need of extra electric power, zero maintenance and ability to perform satisfactorily even under zero gravity environment.
In the present study, we verified the possibility of using commercially available heat pipes to cryogenic applications that do not need new special design and fabricate, quality of performance is uniform due to the mass production and easy availability. The data was accumulated by measuring the thermal performance under various experimental conditions (wick structure, working fluid, filling ratio). Three types of wick structures, that are Groove (G), Sinter metal (S), and combination of them (GS) were tested to investigate the performance change due to difference of wick structures under liquid nitrogen temperature.
The results from this study suggest as follows: it is possible for commercially available heat pipes with working fluid replaced with nitrogen to achieve relatively effective thermal conductivity in the operating temperature range (78 K). The performance rank by the wick structures is as follows in descending order; SG, S and G. The proper amount of liquid fill (100% filling) is giving the best performance of heat pipe.
This study was presented at the 2019 Cryogenic Engineering Conference and International Cryogenic Materials Conference (CEC-ICMC) in Hartford, Connecticut, USA. 21-25 July 2019. I attended the 2019 CEC-ICMC Conference and presented my study by poster presentation on Tuesday, 23 July 2019. The period of time is 2 hours (13:30-15:30, local time). In addition, I prepared my paper to submit as a Conference Proceedings.
High Energy Accelerator Science, Accelerator Science, Ramnarong WANISON